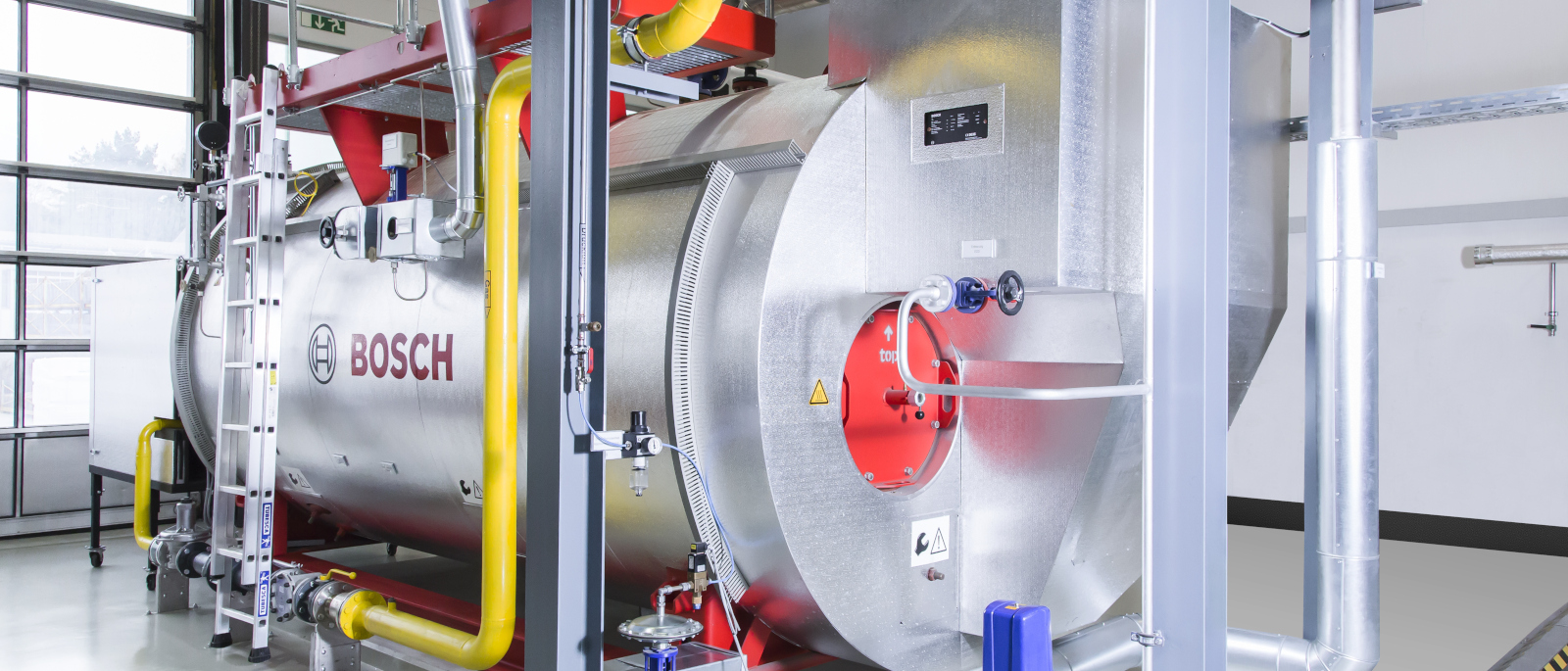
Effizienzsteigerung an Kessel und Anlage
Isolierung
Die Verluste durch Leitung und Strahlung entstehen durch die Temperaturdifferenz des Mediums in Dampfkesseln, Leitungen und Armaturen von der Umgebung.
Die Höhe der Wärmeverluste wird im Wesentlichen durch die Größe der Oberfläche, die Mediums- und Umgebungstemperatur und die Ausführung der Isolierung beeinflusst.
Da diese Verluste nicht leistungsabhängig sind treten sie immer, also auch in Stillstandsphasen, auf und sind damit bei nicht stillgelegten Anlagen oder Anlagenteilen auch 365 Tage im Jahr vorhanden. Besonders in Anlagen, die häufig in Teillast betrieben werden, wirken sie sich negativ auf den Jahresnutzungsgrad der Kesselanlage aus.
Neben der aufwändigeren Untersuchung mit einer Wärmebildkamera können die „Hot Spots“ mit den größten Wärmeverlusten meist auch allein durch das Erspüren von heißen Bereichen, die visuelle Überprüfung der Isolierung oder mittels eines Oberflächen- oder Strahlungsthermometers erkannt und beseitigt werden.
Die Oberflächentemperatur ist allerdings nur bedingt ein Maß für die Höhe der Wärmeverluste. Insbesondere dann, wenn unterschiedliche Oberflächenwerkstoffe miteinander verglichen werden spricht eine niedrigere Oberflächentemperatur mitunter für höhere Wärmeverluste.
Der Grund liegt im Strahlungskoeffizienten der Isolieroberfläche. Ein hoher Koeffizient erhöht die Wärmeverluste, senkt aber gleichzeitig die Oberflächentemperatur. Es ist also der Einsatz eines Werkstoffs mit geringem Emissionskoeffizienten ε vorteilhaft.
Beispiel: |
|
Speisewasserbehälter |
L = 3 600 mm, Ø = 1 700 mm |
Isolierung |
D = 100 mm |
Mediumstemperatur |
103 °C |
Oberflächenwerkstoff1) |
Emissionskoeffizient ε |
Wärmeverluste über |
Oberflächentemperatur |
Aluminium walzblank |
0,05 |
627,5 W |
30,0 °C |
Aluminium oxidiert |
0,13 |
635,5 W |
29,0 °C |
Verzinktes Blech blank |
0,26 |
645,5 W |
27,6 °C |
Verzinktes Blech angestaubt |
0,44 |
655,5 W |
26,3 °C |
Austenitischer Stahl |
0,15 |
637,2 W |
28,7 °C |
Alu-Zink-Blech leicht oxidiert |
0,18 |
639,7 W |
28,4 °C |
Nichtmetallische Oberfläche |
0,94 |
671,2 W |
24,2 °C |
1) nach VDI 2055 Blatt 1 Anhang A8
In bestehenden Anlagen entstehen die größten Wärmeverluste meist durch nicht isolierte Armaturen, durch bei Revision oder Reparatur von Anlagenteilen nicht erneut isolierte Bereiche oder durch, beim Verschieben der Isolierschutzoberfläche, gebildete Wärmebrücken.
Durch die Beseitigung dieser „Hot Spots“ in bestehenden Anlagen kann bereits ein Großteil der Leitungs- und Strahlungsverluste vermieden werden ohne eine komplette Neuisolierung vornehmen zu müssen. Maßnahmen an nicht isolierten Bereichen der Gesamtanlage (z. B. Kessel, Dampf- und Kondensatleitungen, Armaturen, Behältern) stellen eine der wirtschaftlichsten Einsparmaßnahmen in vorhandenen Systemen dar.
Der Wärmeverlust des Kessels selbst kann auch auf einfache Weise im Stillstand ermittelt werden. Nach Außerbetriebnahme des Kessels (z. B. am Wochenende) kann die Druckabsenkung bei geschlossenen Dampf-, Absalz- und Abschlammventilen ermittelt werden. Beginnend bei einem Dampfdruck im Kessel von 10 bar sollte der Druckabfall nicht mehr als 0,2 bar/h betragen. Es ist zu beachten, dass nicht nur die Strahlungs- und Leitungsverluste mit einbezogen, sondern auch die durch den Kaminzug entstehenden Lüftungsverluste gegebenenfalls berücksichtigt werden müssen. Ebenfalls kann das Ergebnis durch nicht dichtschließende Ventile beeinflusst werden.
Der indirekt durch die Druckabsenkung gemessene Wärmeverlust ist jedoch unabhängig von der Ursache vorhanden und sollte vermieden werden.
Die Effizienz der Isolierung kann dabei durch nachfolgende Punkte verbessert werden.
Isolierdicke und Oberfläche
Durch eine Erhöhung der Isolierstärke können die Oberflächentemperatur und der Wärmeverlust reduziert werden. Hier gilt es jedoch eine vernünftige, wirtschaftliche Optimierung zu wählen, da eine Verdoppelung der Isolierstärke keinesfalls eine Halbierung der Oberflächenverluste bedeutet.
Für den Gesamtwärmeverlust spielt neben der Isolierstärke auch die Größe der Oberfläche eine entscheidende Rolle. Hier sind kompakte Kesselbauarten, z. B. im asymmetrischen Design, sowie integrierte Economiser und eine daraus resultierende kleinere Isolieroberfläche von Vorteil.
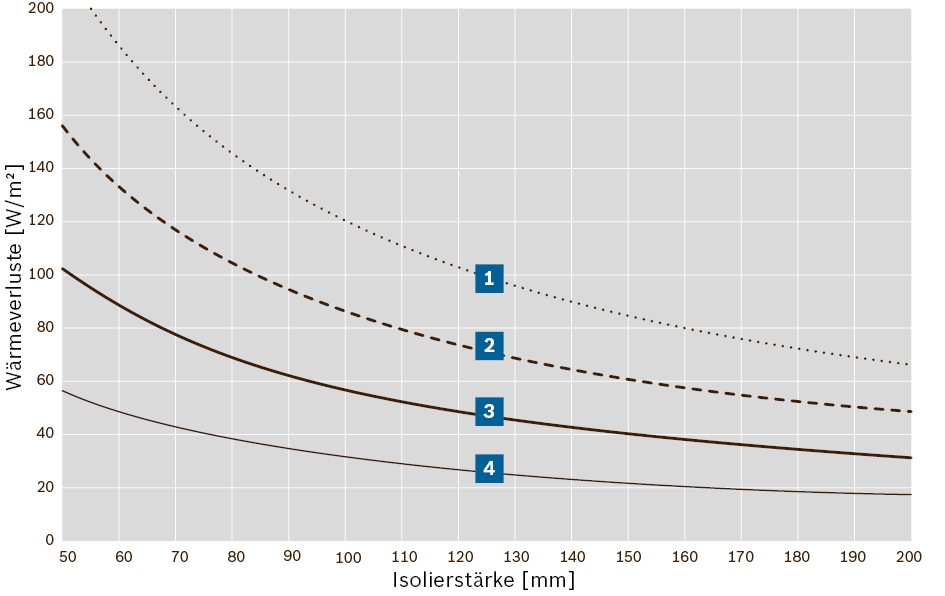
Wärmeverluste über den isolierten Bereich der Behälter- oder Kesseloberfläche
|
Mediumstemperatur: 250 °C (. . . . . .) |
|
Mediumstemperatur: 150 °C (_______) |
|
|
Mediumstemperatur: 200 °C (- - - -) |
|
Mediumstemperatur: 100 °C (_______) |
Die Abbildung oben „Wärmeverluste über den isolierten Bereich der Behälter- oder Kesseloberfläche“ zeigt, dass bei einer Isolierstärke von 100 mm und einer Mediumstemperatur von 150 °C ein Wärmeverlust von etwa 57 W/m² entsteht.
Bei einer Isolierstärke von 150 mm verringert sich dieser um etwa 30 % auf rund 40 W/m². Wird die Isolierstärke auf 200 mm erhöht, reduziert sich der Wärmeverlust gegenüber einer 100 mm Isolierung um 44 % auf 32 W/m².
Dies gilt jeweils nur für die isolierten Bereiche ohne Wärmebrücken. Da die Verluste über diese Brücken schnell die Verluste im gut isolierten zylindrischen Bereich überschreiten können, sind sie stets mitzubetrachten und möglichst zu minimieren.
Isolierung von Rohrleitungen
Die durchgehende Isolierung von Rohrleitungen mit heißem Medium ist inzwischen in allen Anlagenteilen zur Energieeinsparung und zum Arbeitsschutz verpflichtend vorgeschrieben (z. B. Energieeinsparverordnung). Bei der Entscheidung für eine bestimmte Isolierdicke sollten jedoch nicht nur die Vorschriften sondern vor allem die Wirtschaftlichkeit ausschlaggebend sein.
Anhand des folgenden Diagramms kann in Abhängigkeit der Mediumstemperatur, des Rohrdurchmessers und der Isolierstärke sowohl der absolute Wärmeverlust pro Meter unisolierter Rohrleitung (linke Ordinate), wie auch der Einsparfaktor einer isolierten Rohrleitung (rechte Ordinate) bestimmt werden.
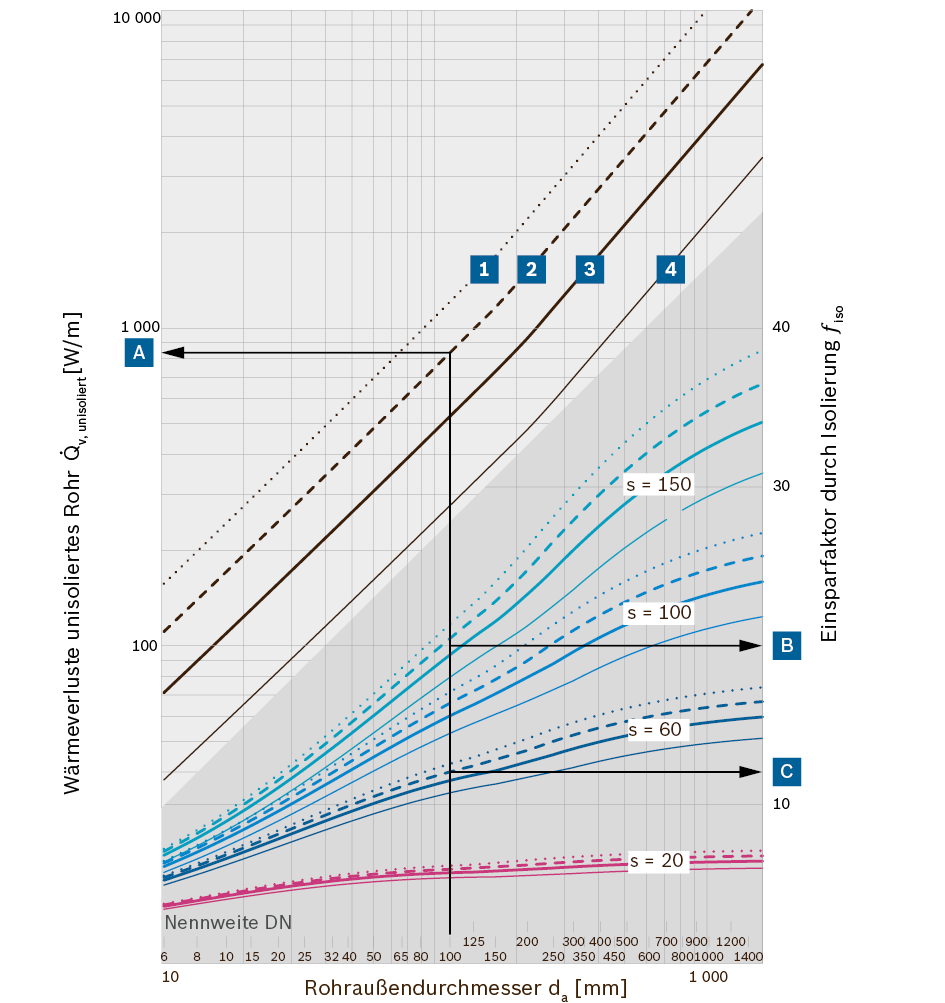
Einsparfaktor durch Isolierung und Wärmeverluste an Rohrleitungen
|
Mediumstemperatur: 250 °C (. . . . . .) |
|
Mediumstemperatur: 200 °C (- - - -) |
|
Mediumstemperatur: 150 °C (_______) |
|
Mediumstemperatur: 100 °C (_______) |
|
Isolierstärke s = 150 mm |
|
Isolierstärke s = 100 mm |
|
Isolierstärke s = 60 mm |
|
Isolierstärke s = 20 mm |
|
Wärmeverlust im unisolierten Zustand |
|
Einsparung durch Isolierung |
|
Einsparung durch Isolierung |
Die Berechnungen für das oben stehende Diagramm „Einsparfaktor durch Isolierung und Wärmeverluste an Rohrleitungen“ erfolgen in Anlehnung an die VDI 2055 Blatt 1: Unisoliertes lackiertes Stahlrohr, Isolierung Mineralwolle, Isoliermantel Aluminium Walzblech, horizontale Rohrleitung, Umgebungstemperatur 20 °C.
Für eine Dampfleitung mit einer Länge von 100 m ergibt sich durch eine Erhöhung der Isolierstärke von 60 mm auf 150 mm eine Einsparung von rund 920 € pro Jahr (bei angenommenen 8 000 Betriebsstunden und 4,5 ct/kWh Energiekosten).
Jeder Meter unisolierte Rohrleitung kostet hier über 300 € im Jahr.
Beispiel |
Stärke der Isolierung |
Wärmeverlust der Rohrleitung |
Gesamtwärmeverlust1) |
Einsparung absolut2) |
Einsparung prozentual2) |
Eingesparte Kosten2) |
A |
unisoliert |
837,0 |
669 600 |
--- |
--- |
|
B |
s = 60 |
66,4 |
53 120 |
--- |
--- |
|
C |
s = 150 |
40,8 |
32 640 |
20 480 |
38,6 |
921,60 |
Einsparpotential durch Erhöhung der Isolierstärke am Beispiel einer Dampfleitung
1) Bei 100 m Rohrlänge und 8 000 Betriebsstunden/Jahr
2) In Bezug auf die Dicke der Isolierung s = 60 mm
Minimierung von Wärmebrücken
Wärmebrücken treten immer dann auf, wenn metallische Verbindungen mit einer sehr guten Wärmeleitfähigkeit die Isolierung durchbrechen. Dies ist z. B. bei Stutzen, Kesselstühlen oder Bühnenkonsolen der Fall.
Besonders im Bereich des Isolierschutzmantels ist darauf zu achten, dass die funktionsbedingt notwendigen Durchdringungen keinen direkten Kontakt zum Isoliermantel haben, da an diesen Stellen sonst Wärmebrücken entstehen und zu einem Energieverlust führen. Bereits eine einfache Umwicklung von Stutzen mit einem Isoliergewebe kann dies zuverlässig verhindern. Elemente, die der Verbesserung der Statik und Steifigkeit dienen, sollten innerhalb der Isolierung liegen und leiten dann auch keine Wärme nach außen zum Isolierschutzmantel.
Ebenso sollten bei zylindrischen Mänteln keine Abstandshalter eingesetzt werden, da diese ebenfalls wie Wärmebrücken wirken. Die Wärmeleitung von der heißen Kesseltrommel zum Isolierschutzmantel ist unterbunden und die Wärmedämmung der Isoliermatte ist vollflächig wirksam.
Isolierte Revisionsöffnungen
Dampfkessel unterliegen wiederkehrenden, inneren Überprüfungen durch die zuständigen Überwachungsorganisationen. Die dafür erforderlichen Revisionsöffnungen wie Hand-, Kopf-, oder Mannlöcher erfordern Durchbrüche im Isoliermantel. Diese Durchbrüche werden isoliert und mit abnehmbaren Isolierdeckeln verschlossen.
Auch die Revisions- und Reinigungsöffnungen an den Abgassammelkammern und Economisergehäusen werden mit der gleichen Isoliertechnik verschlossen, so dass keine erhöhte Strahlungswärme an den Revisionsöffnungen verloren geht. Beschriftungen weisen auf darunterliegende Revisionsöffnungen hin.
Besonders nach Revisionen oder wenn die Isolierdeckel aus anderen Gründen entfernt wurden, ist darauf zu achten, dass die Revisionsöffnungen auch erneut isoliert werden.
Der Wärmeverlust einer nicht wieder verschlossenen Revisionsöffnung mit etwa 0,5 m² Fläche bedeutet bei einem Betriebsüberdruck von 10 bar und einer Temperatur von 185 °C einen Energieverlust von etwa 15 kWh pro Tag.

Abnehmbare Isolierungen an Revisionsöffnungen (UL-S mit integriertem Economiser)
Isolierte Armaturen
In Dampfkesselanlagen finden sich an vielen Stellen Armaturen, die für die Bedienung und Wartung der Anlage notwendig sind. Aus Montage- oder Kostengründen oder aus unterschiedlichen Liefergrenzen wird auch bei Neuanlagen immer noch oft auf die Isolierung von Armaturen oder Übergangsflanschen verzichtet. Ebenso sind in Bestandsanlagen häufig nicht isolierte Armaturen anzutreffen.
Diese unisolierten Bereiche verursachen jedoch einen sehr hohen Energieverlust. Zur Abschätzung des Energieverlusts einer unisolierten Armatur kann folgende Tabelle dienen.
Rohr-Nennweite |
DN 50 |
DN 65 |
DN 80 |
DN 100 |
DN 125 |
DN 150 |
DN 200 |
DN 250 |
|
Länge nach EN 558 Reihe 1 |
[mm] |
230 |
290 |
310 |
350 |
400 |
480 |
600 |
730 |
Wärmeverlust unisoliert |
[W] |
224 |
343 |
419 |
586 |
795 |
1 119 |
1 800 |
2 728 |
Wärmeverlust isoliert |
[W] |
21 |
27 |
29 |
33 |
43 |
58 |
88 |
127 |
Einsparung |
[W] |
202 |
316 |
390 |
553 |
752 |
1 061 |
1 712 |
2 601 |
Wärmeverlust bei 8 000 Bh/a |
[kWh/a] |
1 619 |
2 527 |
3 117 |
4 425 |
6 018 |
8 489 |
13 693 |
20 810 |
Einsparung bei 4,5 Ct/kWh |
[€/a] |
73 |
114 |
140 |
199 |
270 |
382 |
616 |
936 |
Wärmeverluste und Betriebskosten von unisolierten Armaturen (Mediumstemperatur 200 °C)
Hinweise zur Tabelle:
- Mediumstemperatur 200 °C
- Berechnung der Rohrleitungswärmeverluste in Anlehnung an VDI 2055 Blatt 1
- Umrechnung der Wärmeverluste der Rohrleitungen in Wärmeverluste der Armaturen mit Längenfaktor 1,6 für isolierte Armaturen und Längenfaktor 2 für unisolierte Armaturen. (Somit ergeben sich deutlich konservativere Wärmeverluste für unisolierte Armaturen und geringere Einsparungen als über die Berechnung komplett nach VDI 2055 Blatt 1.)
- Armaturenlänge nach DIN EN 558 Reihe 1
Die Reduzierung der Wärmeverluste durch die Dämmung von Armaturen beträgt bei einer Mediumstemperatur von 200 °C und einer Armatur mit Nennweite DN 100 etwa 550 W. Bei einer Nennweite von DN 150 etwa 1 060 W. Bei Kosten für die Dämmung einer Armatur von 100 ... 200 € amortisiert sich diese innerhalb eines Jahres.
Da in einem kompletten Dampfsystem an vielen Stellen Armaturen benötigt werden, beträgt das Gesamtpotenzial durch Isolierung der Armaturen des Dampf- und Kondensatsystems durchschnittlich etwa 1 ... 5 % des Brennstoffverbrauchs.